Endbore Jig
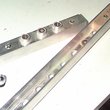
The body is 3/4" architectural channel milled so that the channel is 19.5mm to fit over the typical 19.4mm melamine panel. The channel is drilled with 1/2" holes 32mm apart. The holes accept special bushings that come with any desired inside diameter. These are high quality bushings used in metalworking applications. They have ridges around the perimeter as well as a clamp ring to hold them in place. The MDF stop blocks are located with 5mm sleeves and clamped in place with M4 pan head screws into the sleeves.
The smaller jig is set up with stops at 22.5mm for drilling nailer and toe kick rails (19mm X panels and system holes as construction holes). Depending on what I am making I use 5, 7, and 8mm end holes. With this jig it is easy to swap bushings for the job at hand.
I like the channel idea but it is not real flexible if using melamine and plywood as melamine is a bit over 3/4" and plywood is under. Its not very elegant but you can add masking tape to the inside of the channel to narrow the opening. One thought is to use angle stock, instead of channel, with the bushings centered 9.5mm from the inside corner of the L... Like this (WIP).
Comments [ new ]
- Re: Endbore Jig
- Posted by john on Thursday, 04-Mar-2010
Did you have a machine ship bore out your material on the aluminum jig ?
[ reply | link ] to this. Go to [ topic | top ]
I like the side drill jig, but not sure how to assure 100% direct right angle at all times ? Is that an old lathe head ?
I love your blog.
Thanks,
-dfense- Re: Endbore Jig
- Posted by Dave on Thursday, 04-Mar-2010
I marked the channel with a tape measure and center punch, then bored it using a drill press with the channel against a fence. I've now got a milling machine but it only has something like 8 or 9" of travel and I've had mixed results extending that through the use of locating pins and drill bushing fixtures.
[ reply | link ] to this. Go to [ parent | topic | top ]
The ShopSmith (I added a label to the image link) has a tilting table so it is possible to get 90 degree holes. On my boring machine I chuck drill rod and use spacers like feeler gages to set the head so that the bits are parallel to the table.
I have been playing around with ideas for a better jig. The problem with any extruded aluminum is that, while pretty straight, its neither perfectly square or flat. My current thoughts are a heavy (at least 1/4") over sized channel with bushings 9.5mm from a machined 90 degree corner and knobs for clamping on the opposing face.